Plastic extrusion for large-scale custom plastic parts
Plastic extrusion for large-scale custom plastic parts
Blog Article
Key Advantages and Factors To Consider of Executing Plastic Extrusion in Your Tasks
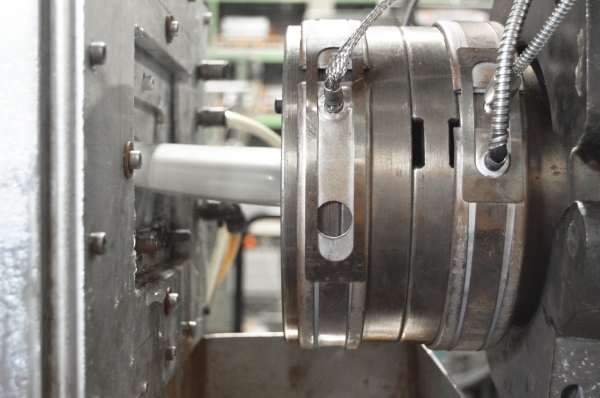
Recognizing the Basics of Plastic Extrusion
Plastic extrusion, a staple in the manufacturing industry, is a procedure that entails melting raw plastic product and reshaping it into a continuous profile. This profile, as soon as cooled down, can be cut into preferred lengths or coiled for later use. The beauty of plastic extrusion exists in its versatility. A wide range of products, from piping to window structures, can be generated. The procedure calls for an extruder, an elaborate device with a heated barrel, a turning screw, and a die at the end. The plastic material, in the form of pellets, is fed right into the extruder, where it's melted and required through the die, taking its shape. The selection of plastic and the style of the die identify the item's characteristics.

The Economic Advantage of Plastic Extrusion
The financial advantage of plastic extrusion lies predominantly in 2 locations: economical material production and advantageous production speeds. With plastic extrusion, businesses can produce high quantities of material at a reduced expense contrasted to various other methods. Moreover, the procedure flaunts an excellent manufacturing speed, significantly reducing time and further improving its economic practicality.
Cost-efficient Product Manufacturing
A significant advantage of plastic extrusion is its impressive cost-effectiveness. This production procedure enables constant, high-volume manufacturing with marginal waste, which equates right into reduced expenses. The raw products made use of, typically plastic pellets, are fairly affordable compared to other substances (plastic extrusion). The procedure itself calls for much less power than lots of various other manufacturing techniques, additionally reducing costs. Additionally, the extrusion process permits for a high level of precision in forming the plastic, decreasing the demand for costly post-production changes or corrections. The durability and durability of extruded plastic products usually mean less need for substitutes, contributing to long-term financial savings. All these factors make plastic extrusion a very affordable choice for many tasks, using an appealing balance between expense and efficiency.
Beneficial Production Speeds
While maintaining the cost-effectiveness of the materials, another noteworthy benefit of plastic extrusion lies in its fast production speeds. This effectiveness in the manufacturing process is credited to the continuous nature of the extrusion procedure, permitting high-volume manufacturing in a relatively short time span. The speed of manufacturing directly associates to a decrease in labor costs and a rise in output, therefore improving the total financial viability of the procedure. Furthermore, the hectic manufacturing does not jeopardize the high quality of the end product, making sure constant and reliable outcomes. This combination of cost-effectiveness, top quality, and rate highlights the substantial economic benefit of applying plastic extrusion in various projects.
Flexibility and Modification: The Toughness of Plastic Extrusion
One of the noticeable staminas of plastic extrusion hinges on its versatility and modification capacity. These qualities open up the door to unlimited design opportunities, giving producers the capacity to tailor products to certain requirements. This enhanced degree of customization not just improves product performance however additionally dramatically increases item uniqueness.
Limitless Design Opportunities
Plastic extrusion shines in its capacity to use practically unlimited layout possibilities. This approach offers liberty to create complex profiles and intricate forms, an accomplishment hard to achieve with various other manufacture strategies. Owing to the look at this website liquid nature of molten plastic, the procedure is adaptable sufficient to produce a varied array of measurements, types, and sizes. The plastic can be adjusted to match special specs, permitting the manufacturing of personalized geometries and conference specific client demands. Plastic extrusion can deal with a range of plastic kinds, broadening its application range. This adaptable strategy, therefore, offers a vast array of sectors from building and construction to vehicle, packaging to electronic devices, and past. With plastic extrusion, the layout opportunities are essentially countless.
Enhancing Product Originality
The adaptability of plastic extrusion can substantially boost item originality. This procedure permits designers to experiment with different shapes, sizes, and colors, giving them the flexibility to develop special items that stick out on the market. It is this personalization that lends a distinct identification to every item, distinguishing it from its rivals.
In addition to its visual advantages, the customizability of plastic extrusion also supplies functional advantages. Therefore, plastic extrusion not just improves product originality however additionally its utility and bankability.
Style Limitations in Plastic Extrusion: What You Need to Know
Just how can design limitations potentially impact the procedure of plastic extrusion? While plastic extrusion is functional, layout constraints can stop its benefits. Understanding these constraints is important for efficient application of plastic extrusion in your jobs.
Reviewing the Ecological Influence of Plastic Extrusion
While recognizing layout constraints is a significant aspect of plastic extrusion, it is equally important to consider its ecological effects. The procedure of plastic extrusion entails melting plastic products, possibly releasing damaging gases into the environment. Further, the resulting items are frequently non-biodegradable, contributing to land fill waste. Advancements in modern technology have actually enabled for more environmentally-friendly practices. Making use of recycled plastic products in the extrusion process can minimize environmental impact. Additionally, establishing naturally degradable plastic alternatives can assist reduce waste problems. Assessing these environmental factors is important when implementing plastic extrusion tasks, guaranteeing a balance between efficiency, cost-effectiveness, and ecological obligation.
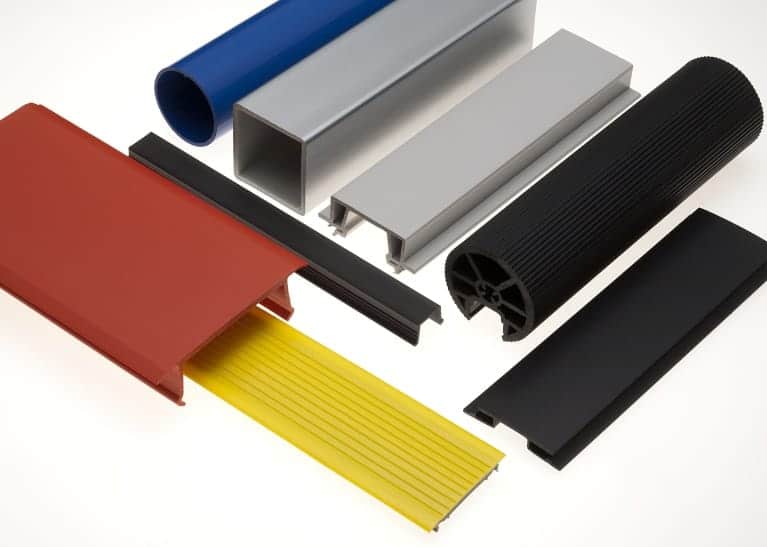
Situation Research: Effective Projects Using Plastic Extrusion
Success stories in the area of plastic extrusion are plentiful, demonstrating both the adaptability and effectiveness of this manufacturing process. plastic extrusion. Another effective situation is the manufacturing of plastic movie for packaging and agriculture. These circumstances illustrate plastic extrusion's critical duty in different sectors, proving to its versatility, cost-effectiveness, and trusted output.
Conclusion
In final thought, view website plastic extrusion provides a economical and effective technique for producing complex forms with marginal waste. Including plastic extrusion right into projects can lead to effective results, as evidenced by countless instance research studies.
Plastic extrusion, a staple discover this in the manufacturing industry, is a procedure that includes melting raw plastic material and reshaping it into a constant account. Plastic extrusion can take care of a range of plastic types, expanding its application scope.Just how can develop limitations potentially influence the procedure of plastic extrusion? The process of plastic extrusion entails melting plastic products, potentially launching hazardous gases right into the setting. Making use of recycled plastic materials in the extrusion procedure can reduce environmental effect.
Report this page